Lubricator
-
The lubrication/
maintenance solution -
Implementation
case example -
About the product
-
Data on the effect of
an implementation of
the lubricator
The lubricator provides a support to Monozukuri (manufacturing) by preventing wear on the site of friction of the machine and equipment, and achieving the improved performance efficiency and the extended life of equipment.
Our history goes all the way back to 1959, when we were officially designated as a manufacturer of vehicle parts for National Railways. We developed our own ultratrace high-performance FUJI MATIC pump to meet the need of transition from manual lubrication to automated lubrication. Starting by the railroad field, we have expanded our business to a variety of industries, and contributed to increase each company's productivity.
The lubrication effects derived from our equipment's power source/air source-free unique mechanism and the high performance/durability have been highly valued and gained the confidence both at home and abroad.
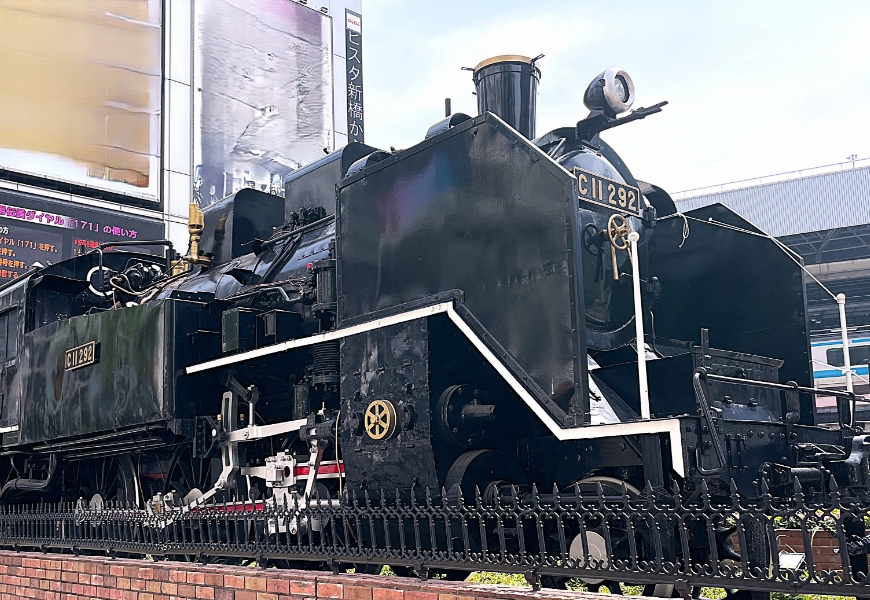
The lubrication/maintenance solution improves production efficiency
and safety as well as solves the problems
experienced on the plant floor.
The stable operation of overhead traveling cranes, chains and gears, which are part of the production line, is the linchpin of the business for manufacturers.
Unexpected stop of their operation would give a significantly adverse impact on the overall production activities, causing a large loss.
(01) Various problems experienced on the plant floor
- Maintenance cost incurred
- Long hours spent for
maintenance operation - Risk of work in high places
- Variability of the work quality
due to personalization of a task - Various problems experienced
opersonalization of a task - Maintenance operation in a small space
We will solve
all these troubles
you may be experiencing!
As a leading company in the lubricator manufacturing business,
FUTEC ORIGIN has supported the “worldwide Monozukuri”
behind the scenes
for almost 70 years.
FUTEC ORIGIN continues to help solve the problems
that the companies face
since we have a wealth of product lineup that takes care of different parts,
including flange, rail, wire and gear
of the crane as well as conveyor chain.
-
Economical benefits
-
The lubrication/maintenance operation used to be performed manually is automated to save manpower.
-
The lubricator extends the life of the machine, substantially reducing the replacement cost.
-
The lubricator reduces the frequency of replacing wheels and rails, etc., decreasing the downtime.
-
-
Safety/environmental benefits
-
The lubricator prevents accidents and downtime of the crane caused by wear of flange/rail.
-
The lubricator improves safety by preventing accidents, such as falling from height or getting caught in a machine, that are likely to occur in manual lubrication.
-
The lubricator not only reduces crane noise, but also reduces electricity consumption with decreased electrical resistance and CO2 emission, ultimately contributing to relieve some environmental burden.
-
Implementation case example
For many years, FUTEC ORIGIN's machine and equipment have been used in major manufacturing scenes,
including iron & steel, shipbuilding, port & harbor and automobile, etc. at home and abroad.
FUTEC ORIGIN continues to support the "worldwide Monozukuri" from behind the scenes.
(01) The Monozukuri scenes where FUTEC ORIGIN's lubricators play active roles
This is an example where everything starts at an ironworks.
The refined/processed iron materials are transported by rail from ironworks to manufacturing floors
where the materials are turned to a variety of products.
Those products are shipped from a port to the world.
FUTEC ORIGIN's lubricators and other products play active roles at each stage of this process.
(02) Fitting equipment for FUTEC ORIGIN's products and the use purposes (as an example)
Industry | Installation site | Subject facility | Use purpose | FUTEC ORIGIN's installable products | ||||||||
---|---|---|---|---|---|---|---|---|---|---|---|---|
CL10 | F | GF | RR/RG | RVF | BF | CF | CR | CS | ||||
iron & steel | Hot strip mill/Cold strip mill | Circular-overhead traveling crane/Trolley | ・Lubrication of crane traveling/ traverse wheels ・Lubrication of crane rail |
|||||||||
Cold strip mill | Lifting-magnet crane | |||||||||||
Coil yard (warehouse) | Coil lifter/coil carrier vehicle | |||||||||||
Pier | Pier container crane | |||||||||||
Steel plant | Casting crane | |||||||||||
Raw material yard | Reclaimer | |||||||||||
Pier | Pier container crane | Lubrication of hoisting wire rope | ||||||||||
Raw material pier | Unloader | |||||||||||
Yard vehicle | Torpedo car | Lubrication of traveling wheels | ||||||||||
Steel trolley | ||||||||||||
Shipbuilding | dock | overhead traveling crane,Goliath crane | Lubrication of crane traveling/traverse wheels | |||||||||
jib crane | Lubrication of crane rail | |||||||||||
Goliath crane | Lubrication of hoisting wire rope | |||||||||||
Port and harbor | Pier | Pier container crane | Lubrication of crane traveling/traverse wheels | |||||||||
Lubrication of hoisting wire rope | ||||||||||||
container yard | transfer crane | |||||||||||
Automobile | all locations | Various types of conveyor chains | Lubrication of conveyor chains |
There are many case examples other than the above.
Please feel free to make an inquiry.
(03)
Product installation case example
(Overhead traveling crane in ironworks)
A cost reduction and extension of operational life of the equipment
were achieved by lubricating the crane wheels.
The cost of replacing wheels and rails due to wear is the highest in the overall maintenance expenses for the crane operation in steel business.
The profitability in the steel business is closely related to the maintenance cost control. A maintenance cost reduction is indispensable to global business.
FUTEC ORIGIN's lubricators are available for both crane rails and crab rails to offer comprehensive antiwear solution.
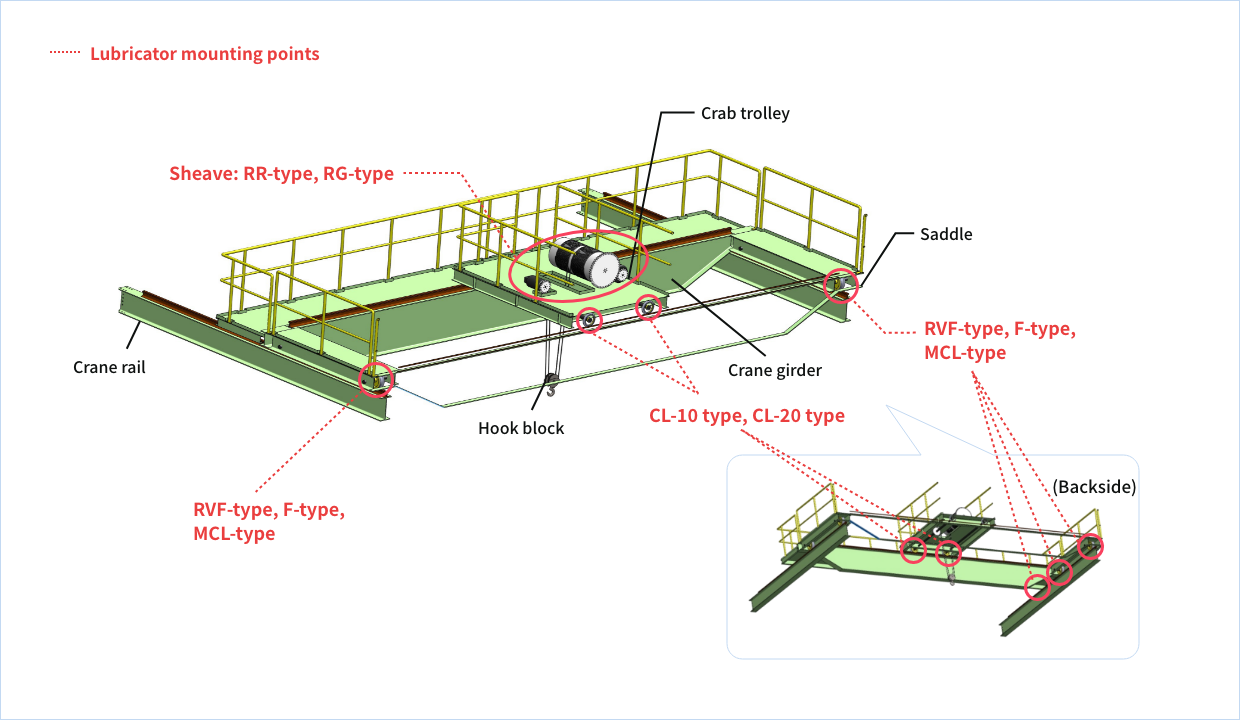
About the product
(01) Product list (partial)
A wide variety of models specialized in industrial cranes, gears, ropes and chains are lined up!
-
Wet-type lubricator
-
Rail lubricator/RVF-type
-
Flange lubricator for cranes/F-type
-
Rope lubricator/RR-RG type
-
Gear lubricator/GF-type
-
Tread lubricator/VF-type
-
Flange lubricator for low-speed vehicles/BF-type
-
Wire rope lubricator
/RWF-type -
(Oil feeder)
Chain automatic lubricator
/CS-type -
(Oil feeder)
Chain automatic lubricating apparatus
/CR-type
-
-
Dry-type antifriction device
*We have products other than those listed above. We also have models having different oil discharge orientation and different mounting brackets.
Moreover, we customize ready-made products and develop new products according to the customer's needs.
Please feel free to make an inquiry.
(02) Selection of equipment based on the lubrication type
Lubrication type | Wet-type (oil) | Dry-type (solid lubricant) |
---|---|---|
Outcome of implementing the lubricator | The equipment life can be extended by 4 - 5 times for wheels or 2 - 3 times for rails. In addition, meandering and travel resistance of the crane can be reduced, lowering the power consumption. |
Flange wear can be reduced by applying lubricant to the wheel flange. |
Use purpose | To reduce wear on flange and rail of traveling wheels | To prevent wear on wheel flange of the overhead traveling crane and oil-incompatible places. |
Lubricant used | Lubricant oil(FUTEC ORIGIN-specified lubricant oil or equivalent) | Exclusive-use lubricating rod (Molybdenum disulfide-based solid lubricant) |
Characteristics | The anti-wear effect is greater than the dry-type. Without the need of power/air source, ultratrace lubricant oil is applied to the friction surface. Since oil discharge is adjustable, an adequate discharge amount can be maintained according to the operating rate. |
Since it uses solid lubricant, the lubricator can be installed at a place incompatible with oil. As the body is smaller than the wet-type, this lubricator is easier to install on small wheels or in narrow spaces. |
What to keep in mind | An adequate oil quantity control is required. | When used outdoors, the lubricant applied on the surface may be washed away by rainwater, etc. |
Maintenance operation | Oil refill and replacement of lubricating wheels. | Needs of lubricating rod |
Key to a successful selection | Select this type for a higher wear-resistant effect. |
Select this type when the installation site is oil-incompatible, too narrow to secure enough space for installation, or for installation on small wheels. |
(03)
Basic construction of a lubricator
(standard package)
The lubricator is comprised of main body,
oil tank, and hose to connect them.
*The tank capacity and the hose length
may be selected according to the use environment.
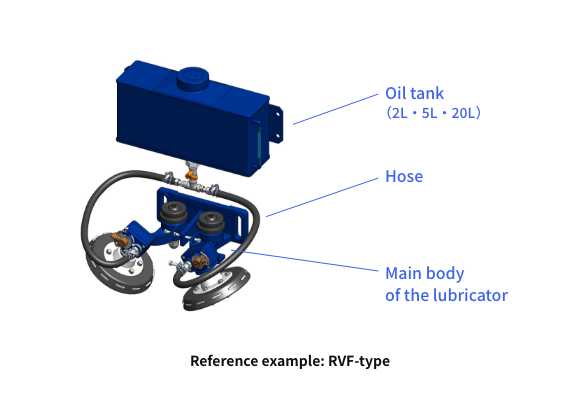
(04) Reasons why companies want to adopt FUTEC ORIGIN's lubrication apparatuses
FUTEC ORIGIN's lubricators help to reduce parts wear by automatically applying adequate lubrication,
and reduce cost by extending the replacement cycle.
Moreover, they save manpower by shortening the time spent for maintenance work,
and reduce dangerous tasks such as working in high places to improve safety of the workers.
The capability of the lubricators to comprehensively support "Monozukuri" in economic,
safety and environmental aspects is the reason why companies want to adopt FUTEC ORIGIN's lubrication apparatuses.
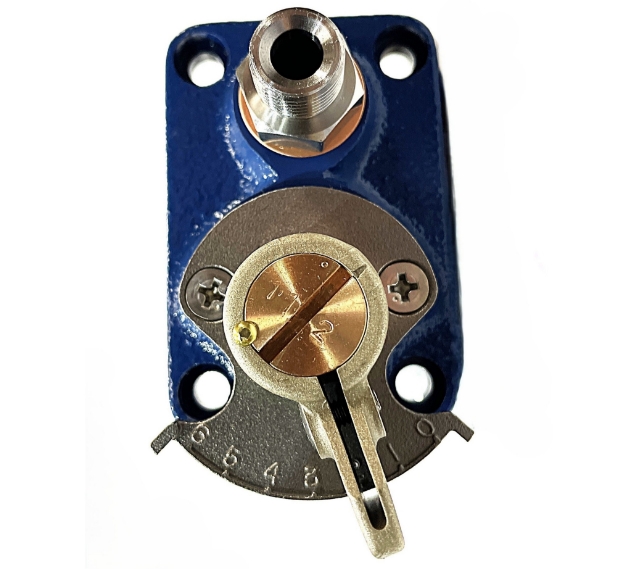
Ultratrace high-performance "FUJI MATIC pump"
Ultratrace high-performance "FUJI MATIC pump", uniquely developed by FUTEC ORIGIN, offers highly effective lubrication. The simple but sophisticated construction of the pump is inimitable, which is incorporated into (*some of) our products as FUTEC ORIGIN's original part. FUTEC ORIGIN's products using this pump are widely used mainly in ironworks around the world. The pump is well-known abroad with its nickname, "FUJI MAGIC pump".
- No power/air source is required
to activate the pump. - The amount of lubricant can be controlled
to the desired level. - The pump discharges the lubricant
in the same way regardless of the rotating direction
(right or left) of the lubricating wheels.
Data on the effect
of an implementation of the lubricator
Here are some of the data related to the use of lubricator, obtained thanks to the cooperation of ironworks.
The data is the evidence of positive effect due to the implementation of FUTEC ORIGIN's lubricators.
(01) Measurement of wear on wheel flange of the crane
The situation prior to implementing the lubricator
When to replace wheels: Replace wheels when the wear limit 14mm is exceeded.
Average life of wheels (prior to implementing the lubricator):
1 year in 2006 and less than 6 months in 2007.
As it turned out, 18 wheels and 8 wheels were replaced
in 2007 and 2006 due to flange wear, respectively.
Flange wear of an average 1.2 to 2.4mm
was detected in a month.
Investigation summary
We conducted some tests on the implementation effects of FUTEC ORIGIN's "Rail lubricator/RVF-1800 type" during the period between December 2007 and April 2008.
The initial measurement of the depth of wear on the flange of eight wheels was conducted on December 2, 2007.
After that, RVF was installed and follow-up measurements were conducted three times during the period.
(Condition of measurement)
Investigated plant | A‘s B Steel Works ※This is real data that we collected, but it has been anonymized for information-protection purposes. |
---|---|
Crane ID | CASTING CRANE |
Operating Hours | 24 HRS |
Diameter of Wheel | 800mm |
Ambient Temp. | 45 DEG. |
CCS | Steel plant |
---|---|
Crane Capacity | 180+50 / 15ton |
Rail Width | CR 120 |
No. of Wheels in the Crane | 8 / SIDE |
Crane Atmosphere | DUSTY |
Inner Collar Thickness in mm
Wheel No. |
Inspection Date | Reduction in 4 months |
Average Rate of Wear & Tear per month |
|||
---|---|---|---|---|---|---|
2007/12/2 | 2008/1/7 | 2008/2/28 | 2008/4/8 | |||
1 | 21.90 | 21.50 | 21.40 | 21.40 | 0.50 | 0.13 |
2 | 23.10 | 22.00 | 21.20 | 20.60 | 2.50 | 0.62 |
3 | 27.10 | 27.10 | 27.00 | 26.90 | 0.20 | 0.05 |
4 | 26.90 | 26.90 | 26.80 | 26.80 | 0.10 | 0.02 |
5 | 18.40 | 18.00 | 17.80 | 17.80 | 0.60 | 0.15 |
6 | 20.10 | 19.40 | 18.40 | 18.30 | 1.80 | 0.45 |
7 | 27.90 | 25.80 | 28.20 | 28.20 | 0.00 | 0.00 |
8 | 28.00 | 28.00 | 27.20 | 26.40 | 0.80 | 0.40 |
(Unit:mm)
Average:0.23
The average depth of wear per month
was controlled to0.23mm.
Outer Collar Thickness in mm
Wheel No. |
Inspection Date | Reduction in 4 months |
Average Rate of Wear & Tear per month |
|||
---|---|---|---|---|---|---|
2007/12/2 | 2008/1/7 | 2008/2/28 | 2008/4/8 | |||
1 | 28.30 | 28.30 | 28.30 | 27.50 | 0.80 | 0.20 |
2 | 27.10 | 27.10 | 27.10 | 26.90 | 0.20 | 0.05 |
3 | 27.10 | 27.10 | 27.10 | 27.10 | 0.10 | 0.03 |
4 | 29.00 | 29.00 | 28.80 | 28.80 | 0.20 | 0.05 |
5 | 33.00 | 32.50 | 32.40 | 32.40 | 0.60 | 0.15 |
6 | 25.10 | 25.00 | 24.80 | 24.80 | 0.30 | 0.08 |
7 | 28.10 | 28.00 | 27.90 | 27.80 | 0.30 | 0.08 |
8 | 30.00 | 29.50 | 29.10 | 28.70 | 1.30 | 0.33 |
(Unit:mm)
Average:0.23
The average depth of wear per month
was controlled to0.12mm.
Conclusion made by A's B Steel Works (excerpted from the Verification Report)
With the use of FUTEC ORIGIN's lubricator, the maximum depth of wear on the wheels is reduced to
0.62mm/month while the expected life of the wheels significantly extends to 22.6 months
(as compared to 6 months to 1 year without the use of the equipment).
It never causes slippage on the wheels, and there is no oil flying to the vicinity or system malfunction due to dust.
No wear on the rail itself has been detected. The oil consumption has been as low as 4.5 litters in 4 months.
The rail lubricator (RVF) offers high performance.
It reduces wear on the wheels, giving a positive effect on our performance improvement policy for the cranes.
As a conclusion, we recommend a step-by-step implementation of FUTEC ORIGIN's lubricator in other sections.
(02) Changes in the frequency of crane wheel replacement due to flange wear
We investigated the frequency of wheel replacement due to flange wear for different cranes
used in the steel making/oxygen converter processes in the span of 8 years between 2006 and October 2014.
Investigated plant | A‘s C Steel Works ※This is real data that we collected, but it has been anonymized for information-protection purposes. |
---|---|
CCS | Steel making/oxygen converter processes |
Investigation period | 2006 - October 2014 |
Crane ID | Teeming Crane |
---|---|
Slag Pot Handling | |
Scrap Handling | |
Hot Metal Charging |
Name of the crane | 2006 | 2007 | 2008 | Rail lubricator/Implementation of RVF1800 | |||||
---|---|---|---|---|---|---|---|---|---|
2009 | 2010 | 2011 | 2012 | 2013 | 2014 | ||||
Teeming Crane | 7 | 4 | 4 | 0 | 0 | 0 | 0 | 4 | 0 |
Slag Pot Handling | 3 | 0 | 5 | 0 | 1 | 5 | 1 | 1 | 1 |
Scrap Handling | 1 | 0 | 1 | 0 | 0 | 2 | 2 | 1 | 0 |
Hot Metal Charging | 0 | 0 | 0 | 0 | 0 | 0 | 0 | 1 | 0 |
Total | 11 | 4 | 10 | 0 | 1 | 7 | 3 | 7 | 1 |
Average | 8.3 times/year | 3.2 times/year(-61%) |
Outcome of implementing the lubricator
After implementing the Rail lubricator RVF-1800 in 2009,
the average frequency of replacement has significantly reduced to less than 40%,
from 8.3 time/year to 3.2 times/year,
which ultimately reduced the maintenance cost and saved time.