Sheet counter
Let's make a change to the "traditional"
visual counting
The mainstream of sheet-count management is visual counting and weight measurement.
In the past, an extra sheet sometimes mixed up in the shipment due to miscount was not a subject for complaint.
However, recently we are expected to make sure to deliver the exact number of sheets as ordered.
With the traditional visual operation, it is becoming harder to maintain such expected accuracy.
This sheet counter can solve the problem. The device may be easily operated by any operator alone.
Press the button and the counting completes in just 3 seconds.
Try and experience the redefined "counting" with this sheet counter.
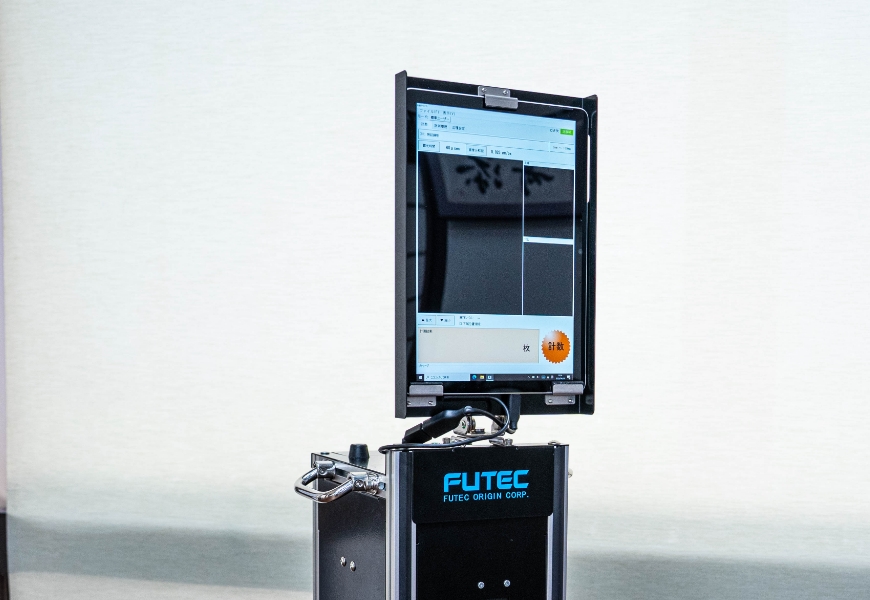
About the product
(01) Product list (partial)
A pile of sheet materials is shot with a camera before the sheet count being displayed via image processing.
It is possible to rapidly and accurately check the count with contact or without contact (*) with the sheet materials.
It provides the same accuracy no matter who performs the count operation without a need of prior input of the sheet thickness.
-
Sheet thickness
The device can be adjusted according to the thickness of the product the user deals with. Please consult with us.
-
Maximum height of a pile
520mm (Customizable)
-
Performance
Battery-powered or cable-powered (selectable)
(*) The possible distance from the material varies depending on the quality of the material.
Please consult with us for more detail.
(02) Customization - Example -
The software is customizable according
to each user's operation.
Pass/fail judgment feature
The expected number of the product subject to counting is input to the sheet counter beforehand to be handed over.
The set number can be altered/adjusted according to the type of product and work details.
Upon completion of the count operation, the actual count of the product registered in the sheet counter and the number set beforehand are cross-checked automatically.
Based on the result, pass/fail of the counting is determined.
The result is indicated with symbols "〇(pass)" or "X(fail)" on the application screen so that it is easily communicated to the operator.
The result is also notified to the operator by buzzer sound.
This way, the operator is able to check the judgment right away,
enabling a smooth transition to the next process.
History management
In this system, the required information such as the product name and the model can be registered prior to the count operation.
A method of handing over the information can be selected from the following two methods.
(1) Manual input method: A user directly inputs the product number and the related information to be linked to the count history.
Since the required information can be entered flexibly in this method, it is usable for special products or the managed object.
(2) Automatic input method (machine input): By reading the QR code or bar code, the product information can be imported automatically.
This improves the work efficiency significantly and helps to prevent input errors.
The registered information and the date data will be saved along with the "count history", that is auto-generated for each count.
This enables easy confirmation/management of the information, including "when", "who" counted and "which products" are counted on the history screen.
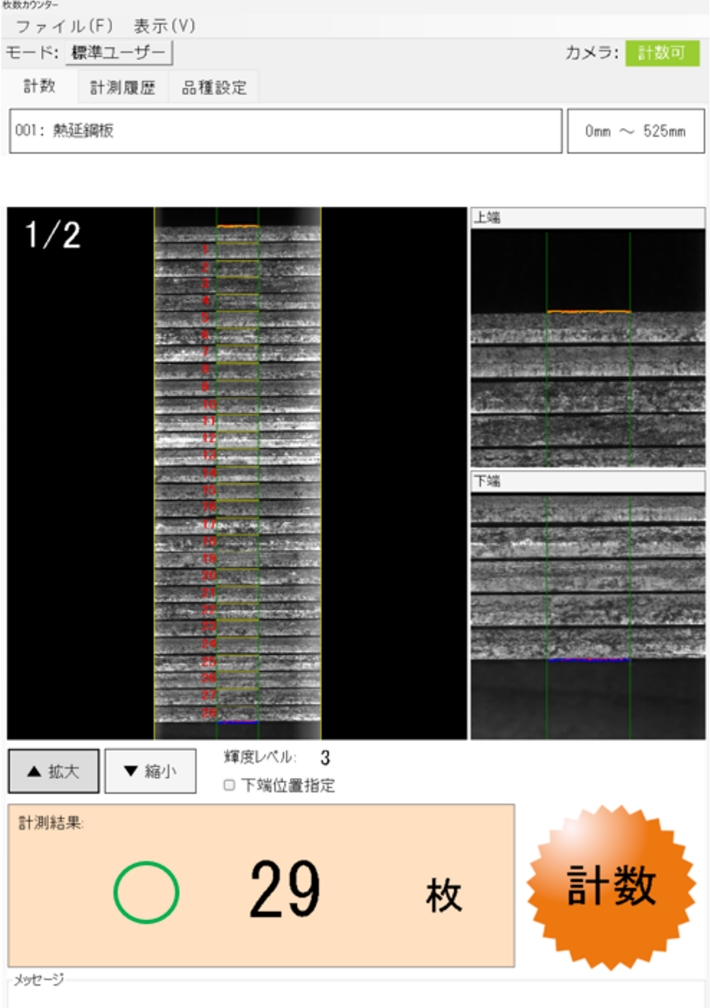
(03) Subject materials
Examples of materials that have been handled in the past
- Ferrous material
- Cold-rolled steel/stainless-steel, etc.
- Non-ferrous metal
- Aluminum, titanium, etc.
- Automobile parts
- Auto body articles, Pressed components
- Carbon material
- Fireproof sheets, black smoke material
- Mica material
- Insulating sheet
- Building material
- Residential wall material, surface treatment material
Problem investigation
-
(01) Problem investigation by visual inspection
While the visual counting is simple and not costly for implementation, it can cause errors easily and lacks operational reliability.
Therefore, what they require is to have an ability to maintain the same "accuracy", "speed" and "outcome" no matter who operates the machine. -
(02) Problem investigation per task
While the automation of count checking using a sensor is underway in the production process, visual counting remains to be the mainstream in other sections.
The automation of sheet count management and man-hour reduction in each section are the important agendas for the future.
(03) Voices after the implementation
- Decrease in
shipment error -
We achieved
"zero shipment errors in a year" for the first time! - Man-hour reduction
-
We reduced the inventory man-hour by
1/3 of the previous man-hour! - Site improvement
- We have diversified workers' tasks by reducing the hours spent for counting operation.
- Prevention of complaints
-
We are able to provide explanations to the customer
using evidence (history/images) left in the sheet counter.