Surface Inspection Equipment
Only solution to protect safety and quality
While the quality improvement of product is increasingly emphasized in the manufacturing industry, some challenges the workers face in the inspection process are becoming more and more apparent, that include a shortage of workers, variability in product quality and growing burden on workers, etc.
Moreover, while the safety and security of visual inspectors are strongly urged, it is becoming more and more difficult to maintain the products' high quality and comply with the "safety first policy" at the same time.
The image inspection device can provide a solution to these challenges.
The device can be an encouraging tool to strengthen the company's competitiveness by achieving "safety and security of workers", "stable product quality" and "improvement of work efficiency" all at the same time.
FUTEC ORIGIN'S image inspection device is currently used in the steel industry and many other manufacturing sites. We hope you get a sense of safety for the future with the use of FUTEC ORIGIN's image inspection device.
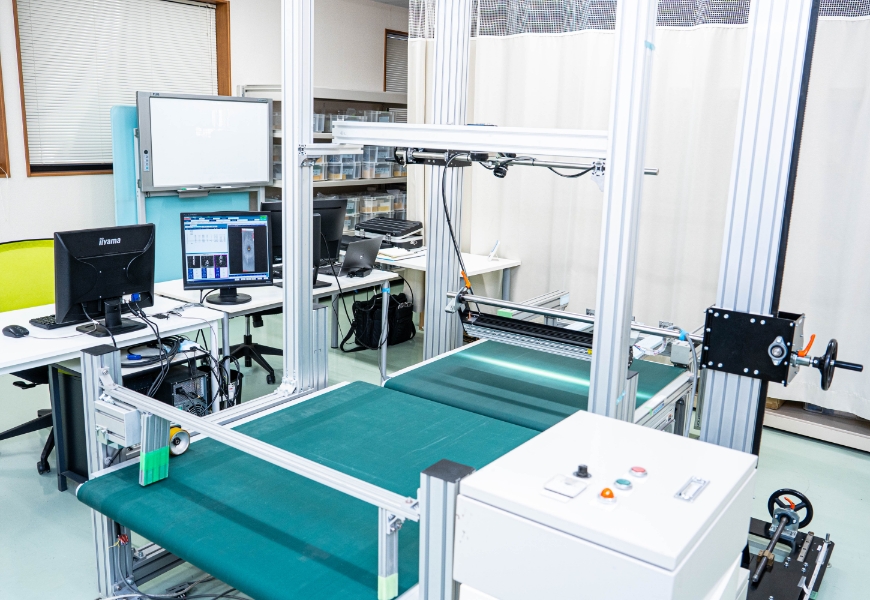
Problem investigation
-
(01) Investigation on problems in the visual inspection
In visual flaw detection on the surface and reverse side of a sheet, some flaws may be overlooked, or it is not possible to perform length inspection. In addition to these quality risks, safety could be a major concern because the workers need to come close to the operating line. One of the major challenges is a difficulty of ensuring accuracy and safety at the same time.
(02) Voices after the implementation
- Ensuring safety
- The workers' safety is secured with the ability to inspect without getting close to the production line.
- Accuracy of detection
- The device is able to detect microscopic flaws and pinholes that are overlooked by human eyes.
- Inspection criteria
- The device is able to quantify the flaw criteria, helping to improve the issues of variability of judgment and personalization of the task.
- A shortage of workers
- The device enables to maintain stable production without worrying about a shortage of workers.
About the product
(01) Product overview
This image inspection device performs a high-speed and high-accuracy detection of flaws on the moving workpieces, including the base material in the steel sheet/coil production line and sheet products in the leveler line.
We also carry pinhole detectors that precisely detect microscopic pinholes on the products being conveyed at high speed.
The detected flaws are displayed on the monitor screen on a real-time basis so that the position information and flaw image can be confirmed immediately.
We will support our customer's safety, product quality and productivity by offering a proposal best suited for the production conditions and the operation.
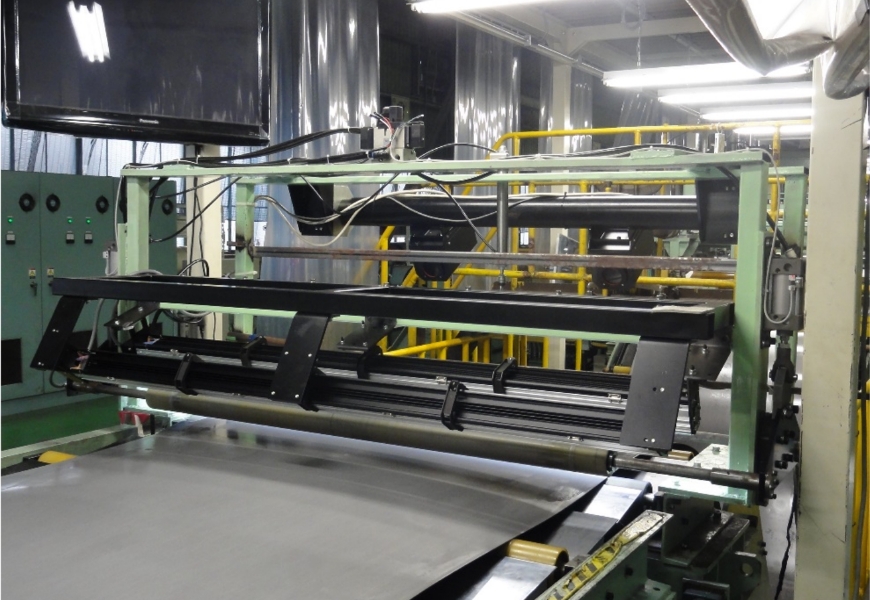
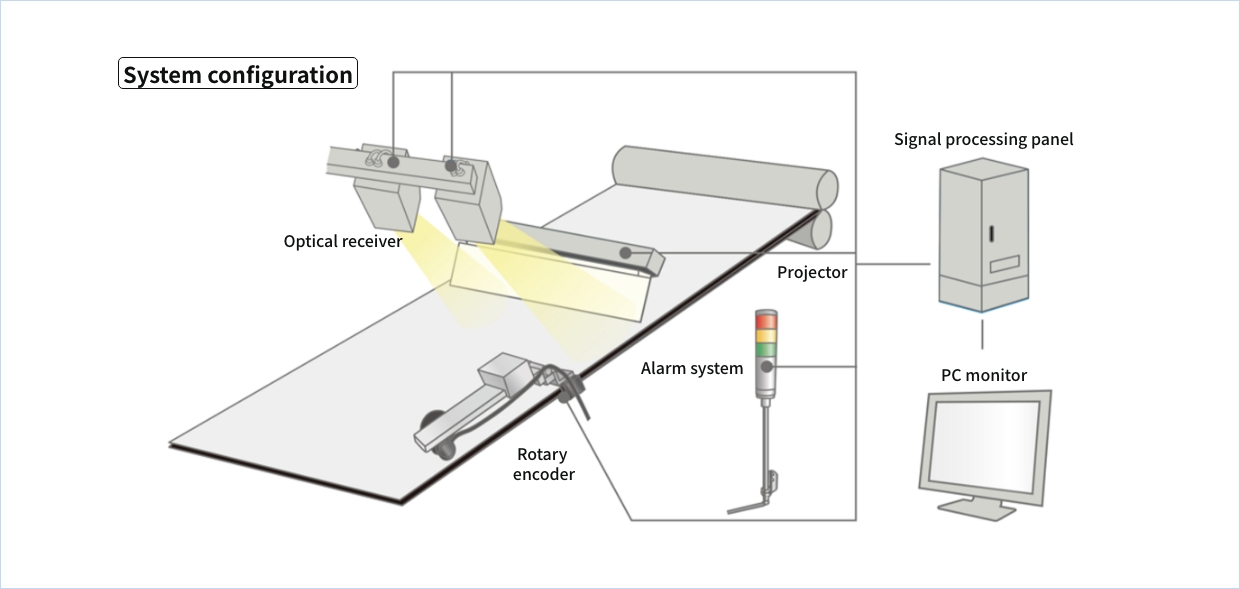
(02) Characteristics
①Example of flaw detection
It detects flaws and pinholes that may be overlooked by human eyes.
Stainless-steel
-
Scab
-
Hair seam
-
Indentation
Magnetic steel sheet
-
Color unevenness
-
Coating patterns
-
Pinhole
Colored steel sheet
-
Seeding
-
Peeling
-
Fading
②Secondary judgment
From the flaws already detected in the primary judgment, a user can register the feature amount of the flaw that is desired to be detected in the secondary judgment so that the device automatically discriminates only those intended flaws.
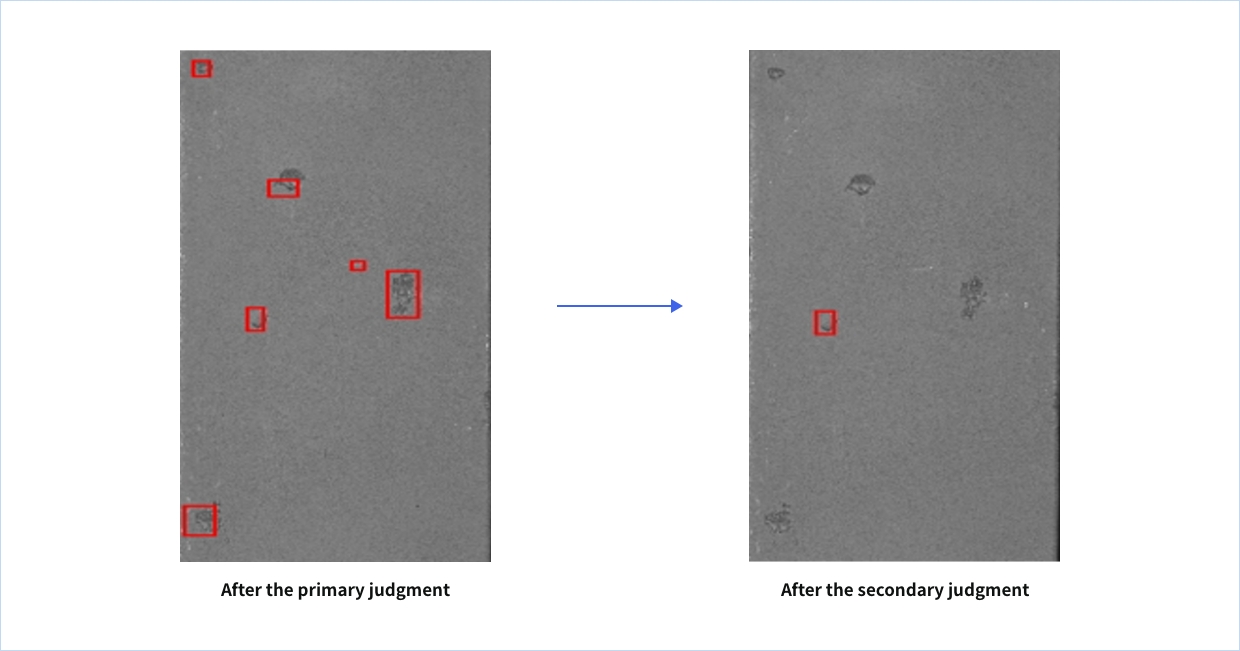
③Periodic/dense judgments
Periodic/dense judgments are made for the flaws detected in the primary judgment. This judgment enables to determine the fundamental cause of occurrence of the flaw.
Periodic judgment
-
1. Prevention of overlooking abnormality By making a period-based comparison with the "proper pattern", minor abnormalities and periodic gap (pitch gap) may be detected.
-
2. Detection of process abnormality - ・When detecting regular defects, such as those in the same position or the same pitch, the abnormality is instantly signaled.
- ・A cause of defect occurrence in the in-house processes can be detected promptly.
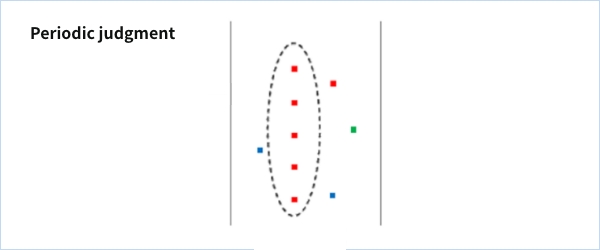
Dense judgment
-
1. Early detection of quality abnormality The problems that are larger and more contagious than individual flaw can be detected early. It catches an "early stage of occurrence" and enables to prevent the defect percentage from worsening.
-
2. Detection of process abnormality There may be in-house equipment malfunction contributing to the occurrence of dense flaw. Using this judgment may enable to perceive some sign of trouble early.
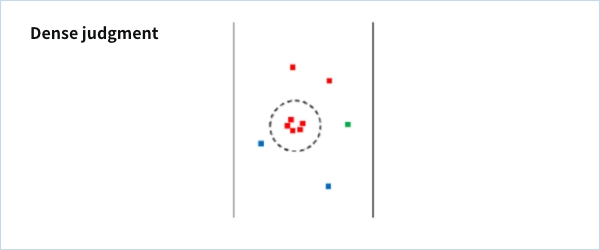
④Coordination with core system/production line
Coordination with core system
With the upper communication facility, it is capable of storing product number and various product information along with inspection data in the inspection history, as well as reviewing "which product was processed/inspected" and "when it was processed/inspected" immediately. In addition, with a coordination with customer's core system, it is capable of centralizing quality control data, including the inspection results and the defect information.
production line
The detected flaws may be classified into 4 ranks by standard. (The number of ranks may be increased by customization.) Particularly, when fatal flaw is detected, the system sends a signal to the line immediately so that the control system set in the production line automatically decreases the speed or stops the line.
This enables to prevent the defects from outflowing and to improve the accuracy of quality control.
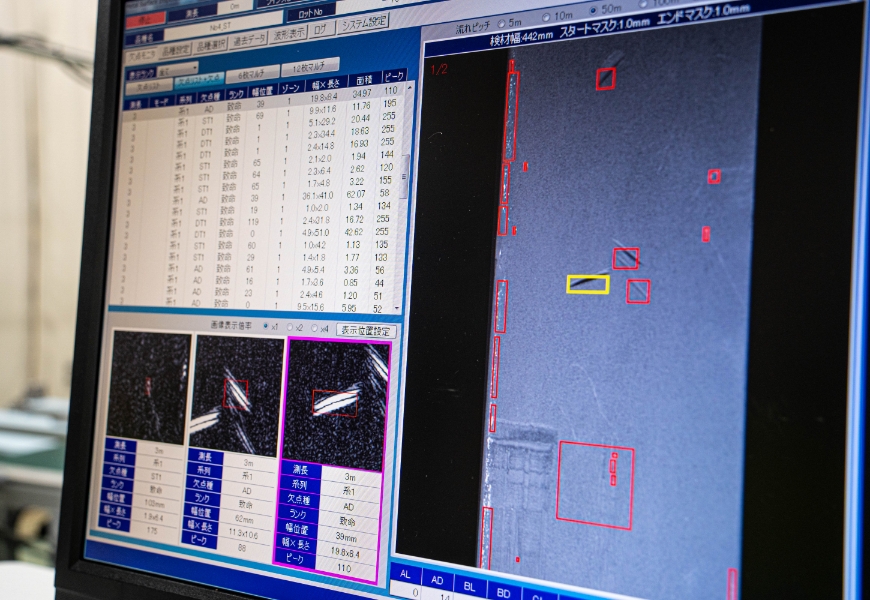
⑤Flexible customization of software
The software may be customized freely in accordance with a customer's request.
We offer one-of-a-kind inspection system by materializing the customer's mental image of the operation.
(03) AI discrimination system (option)
Based on the image detected by the inspection device, the system classifies the types of flaw and makes pass/fail judgment just as humans do.
It is capable of performing automatic discrimination of flaw type without human setting a parameter.
System configuration
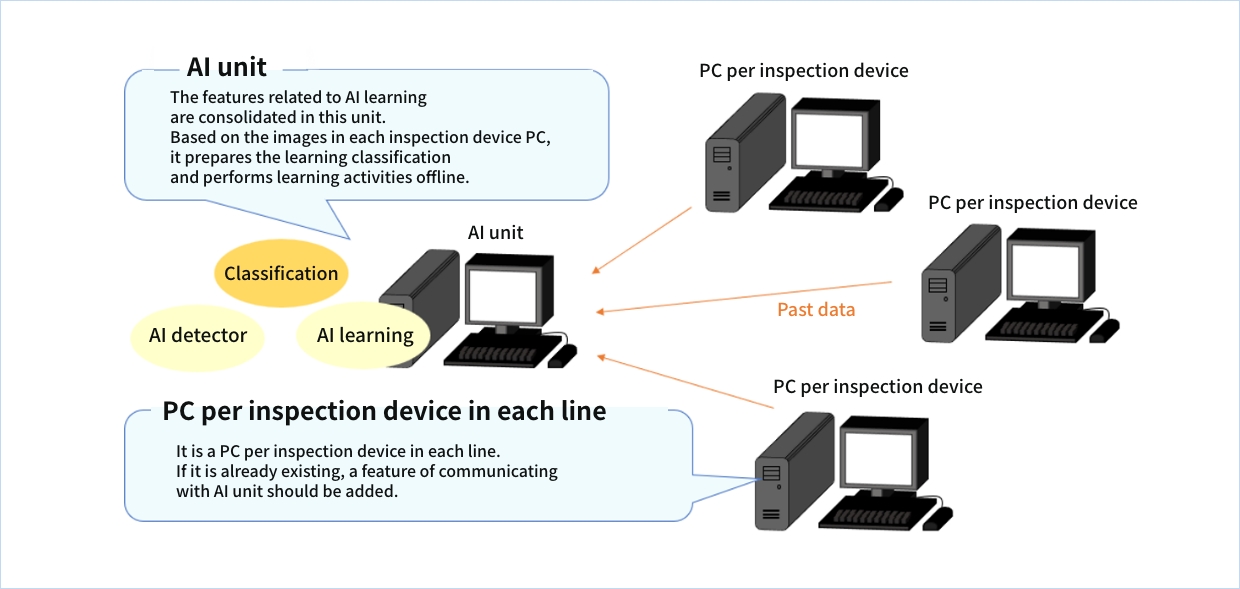
Operation cycle
It repeats a cycle of (1)learning, (2)inspecting, and (3)rejudging.
By repeating the operation cycle over and over again, the accuracy of AI discrimination capability will improve.
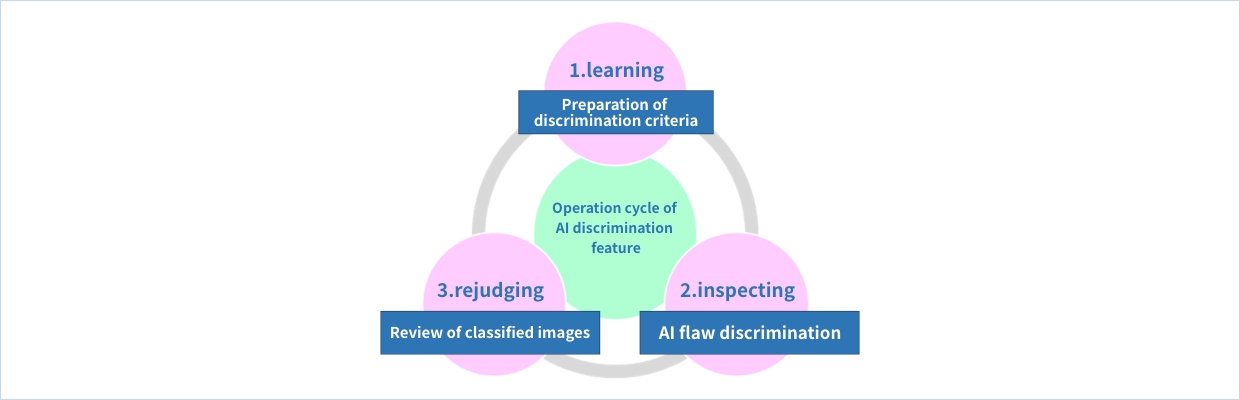
(04) Share in the industry of the company that implemented FUTEC ORIGIN's inspection device
The increasing number of industries implementing the system range from coil center to steel/part manufacturers. The high operability and ease of maintenance are the key to secure repeat customers.