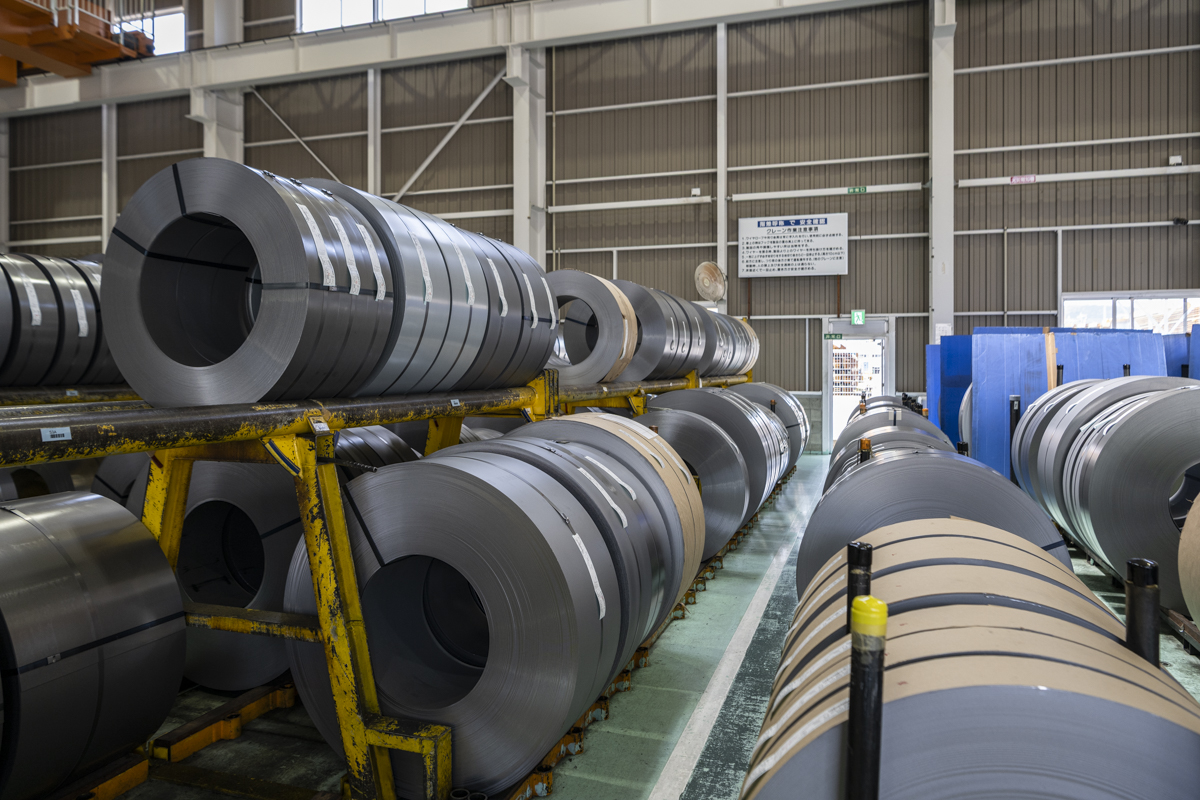
Summit-Benichu Coil Center, Co., Ltd. is one of our clients, which main factory is located in Higashihiroshima City, Hiroshima prefecture. This manufacturer cuts and processes steel sheets, mainly used as automobile parts. The company has implemented FUTEC ORIGIN’s metal surface inspection device in the production line. The metal surface inspection device is a system enabling to automatically inspect flaw on steel sheet surface with special cameras installed in the production line.
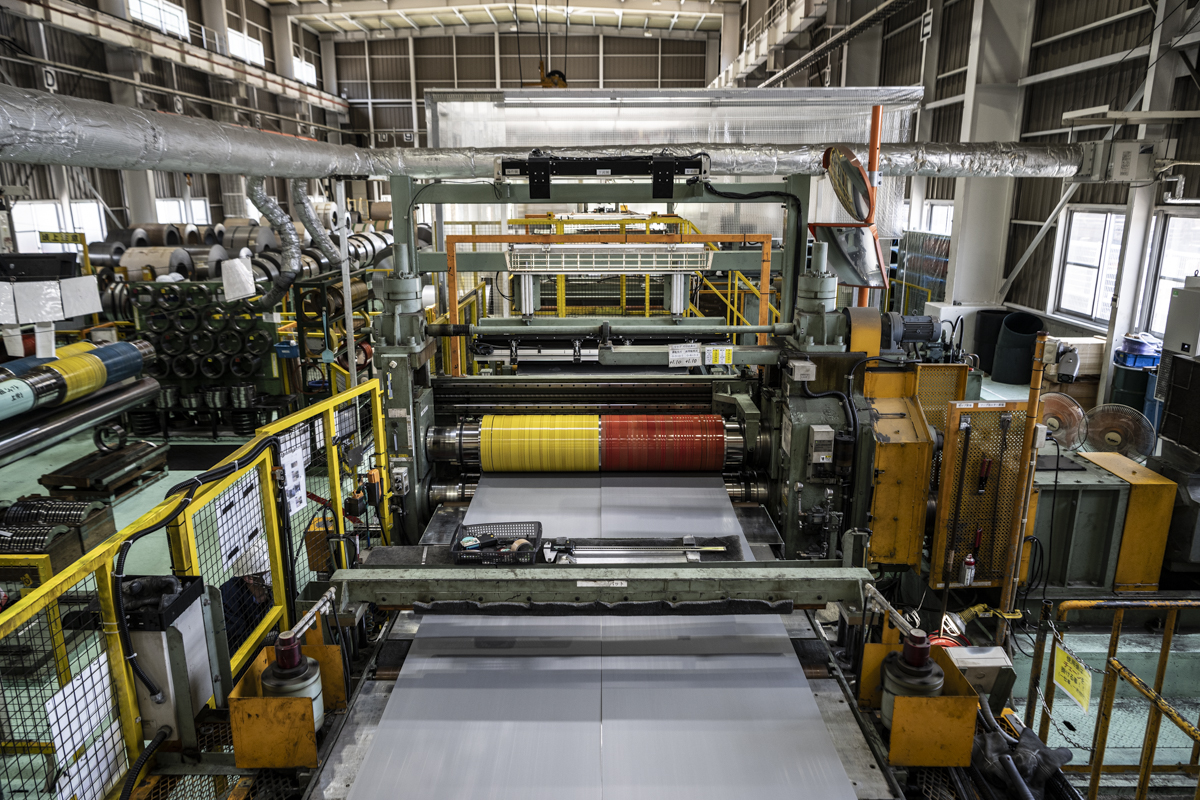
Inside factory of Summit-Benichu Coil Center
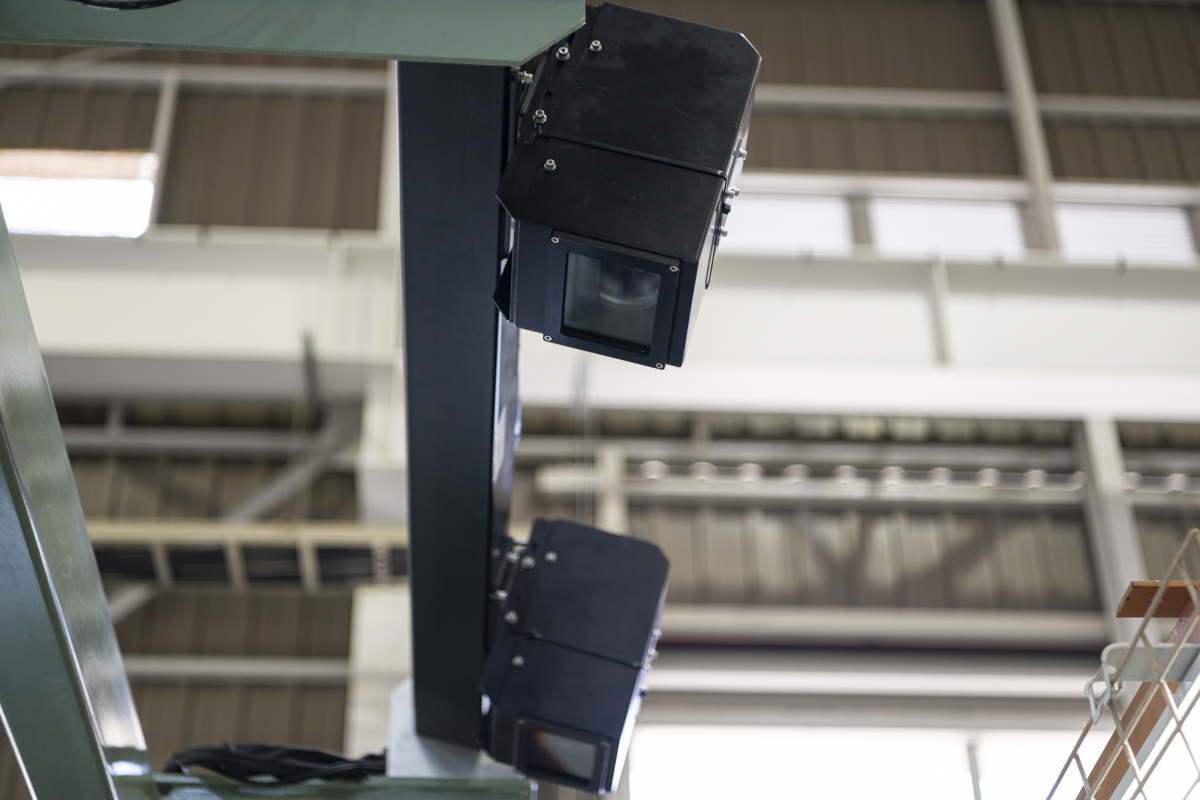
The cameras are installed in the upper and lower parts of the production line where the steel sheets pass through.
Metal surface inspection device implemented to internally perform flaw inspection for stainless-steel coil
Before the company implemented FUTEC ORIGIN’s metal surface inspection device in 2014, what were the challenges they might have in the production line? We interviewed Mr. Takagi, Assistant Manager of the Quality Control Team.
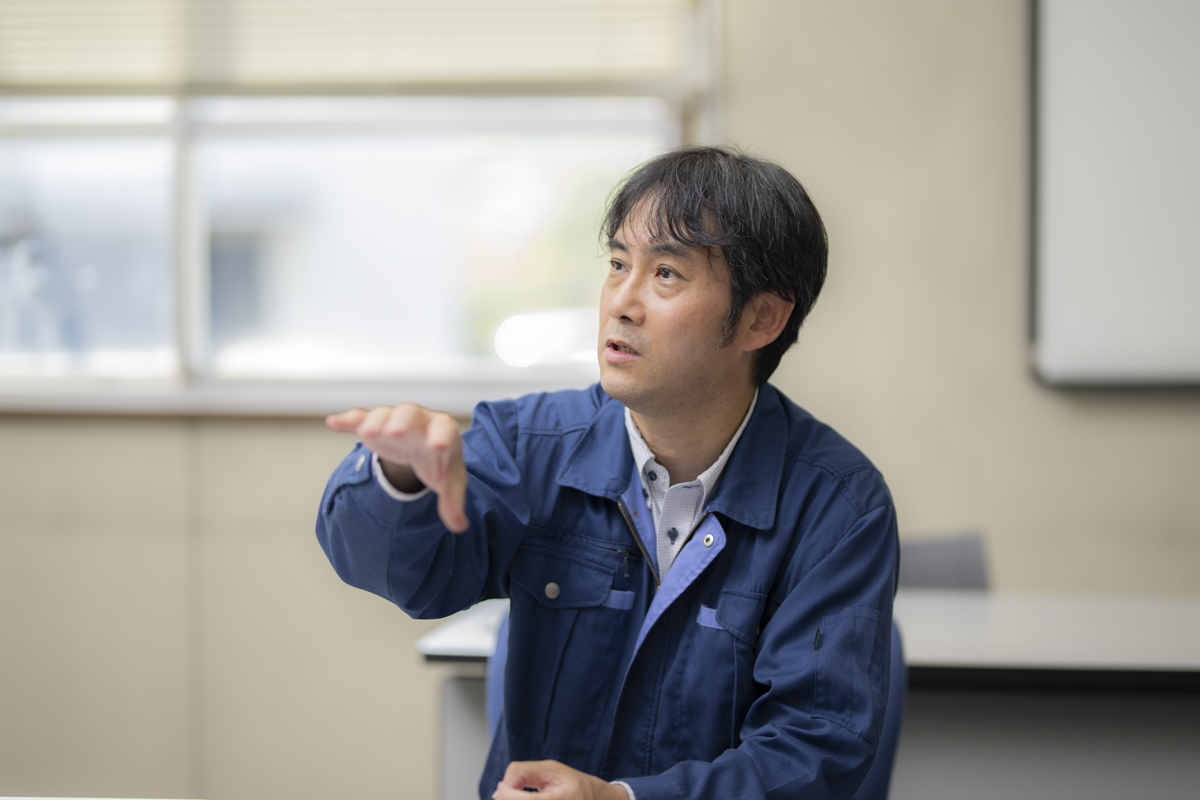
“At the end of the day, the stainless-steel that we are handling is a very sensitive material, and there is no way we may deliver any products with flaw to our clients. The stainless-steel material is cut in pieces in appropriate sizes before delivering to a client. Before implementing FUTEC ORIGIN’s metal surface inspection device, we depended only on visual inspection before delivery. There were some flaw data provided by the stainless-steel manufacturers based on their internal inspection. However, after cutting the original material in pieces, we didn’t have our original flaw data prepared by us. At that time, we only depended on the visual inspection based on the flaw data provided by the manufacturer, and we had no evidence to hand over to a client when asked about the flaw”.
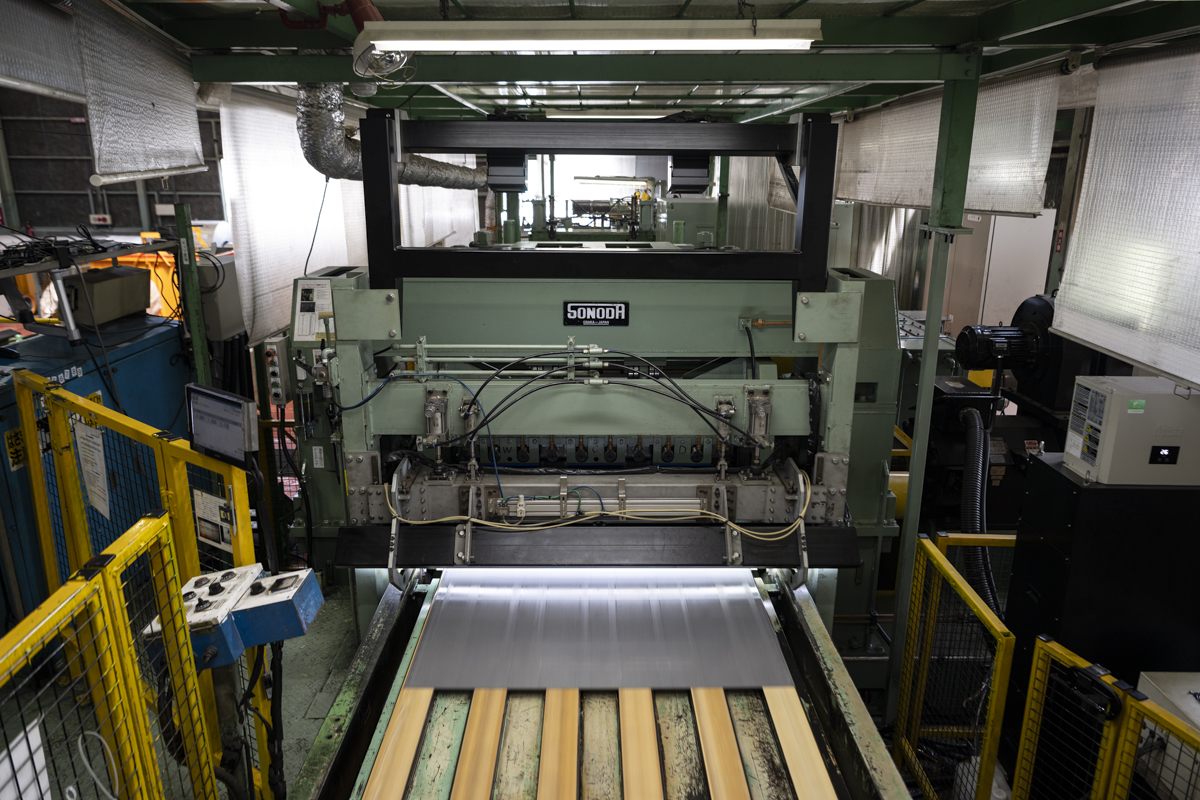
To solve this problem, the company installed FUTEC ORIGIN’s metal surface inspection device. We design the device tailored to each client’s production line; therefore the device can be installed flexibly in the existing line.
Increase of production efficiency and streamlining of operation
Summit-Benichu Coil Center installed the metal surface inspection device more than 10 years ago. Has there been any changes in the plant operation since then? We asked Mr. Kubohara, Manager of the Manufacturing Division 3, about it.
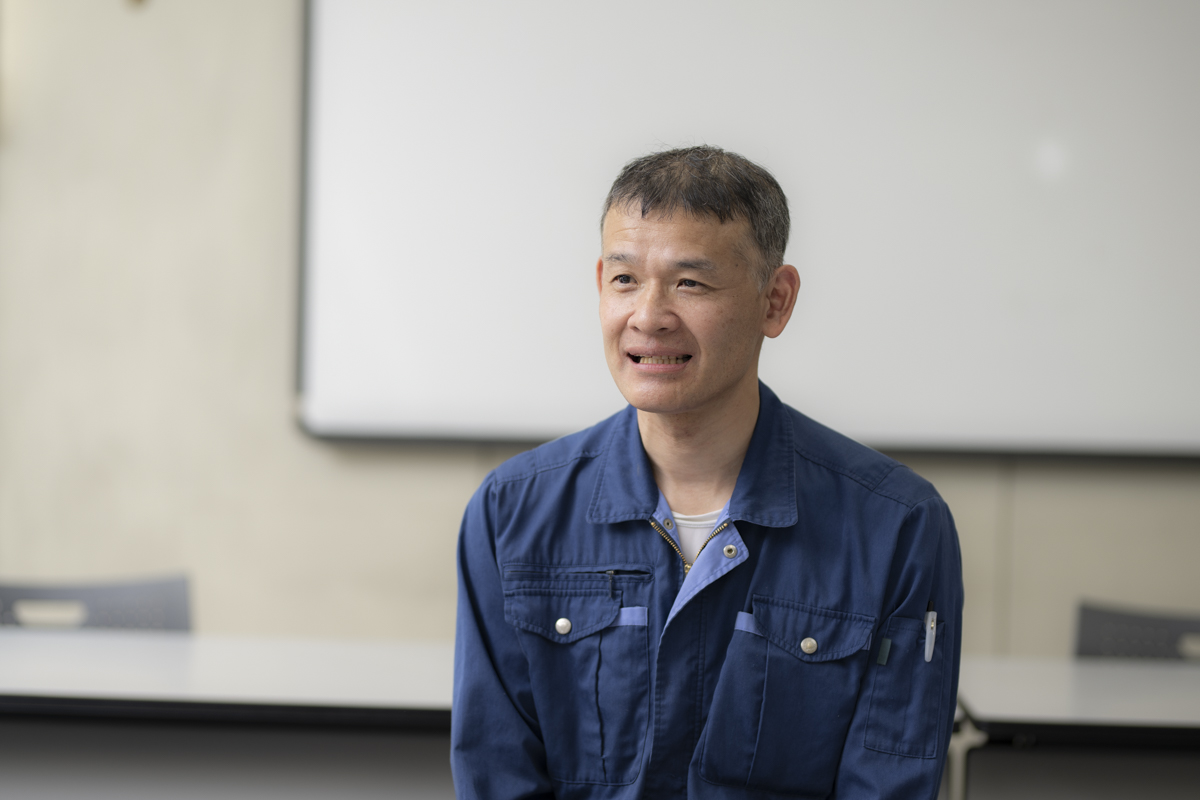
“Before implementing the metal surface inspection device, we used to allocate an employee to the production line for checking flaws visually. It was a hard work because the inspector had to stay in a forced posture only to do a single task. Not only that, every time a flaw was detected, we had to pause the production line, that caused a decrease in speed of production. But now, thanks to the ability of automatic inspection, there is no need to stop the production line. This, by itself, increased the production efficiency by at least 20%, I believe. Needless to say, since we don’t need a visual inspector, we can allocate that personal resource elsewhere to further increase the overall work efficiency”.
Internal flaw inspection offers a great advantage for sales and marketing
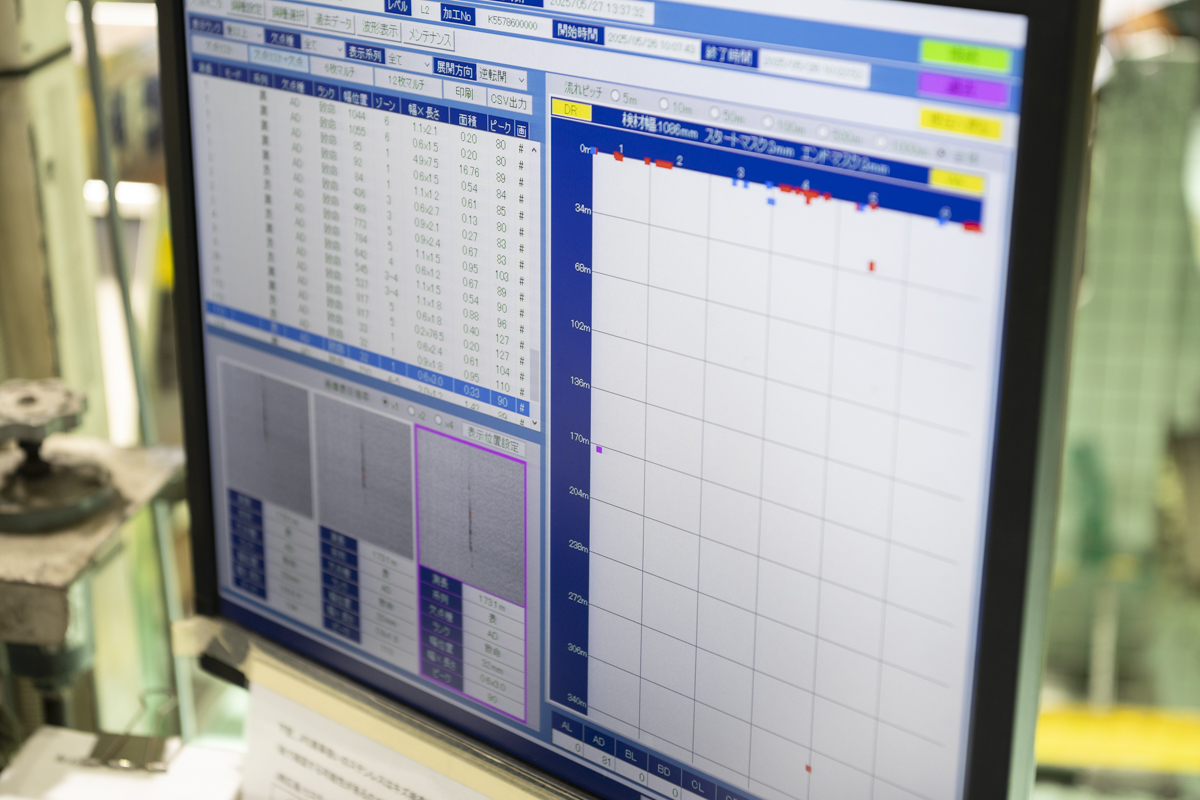
The images captured by the camera are analyzed to instantly display the flaw data.
An improvement of production efficiency is one of the major benefits in implementing the metal surface inspection device. In addition, it seems the fact that the company performs internal flaw inspection itself gives Summit-Benichu Coil Center a huge advantage in persuading the clients in the sales activity.
“Some clients take into account flaw conditions very seriously. For those clients, the availability to submit data obtained in the internal inspection supported by reliable evidence becomes a strength in the sales activity. The data can be immediately printed out from PC. We attach data of the detected flaw, as required to the delivered goods”.
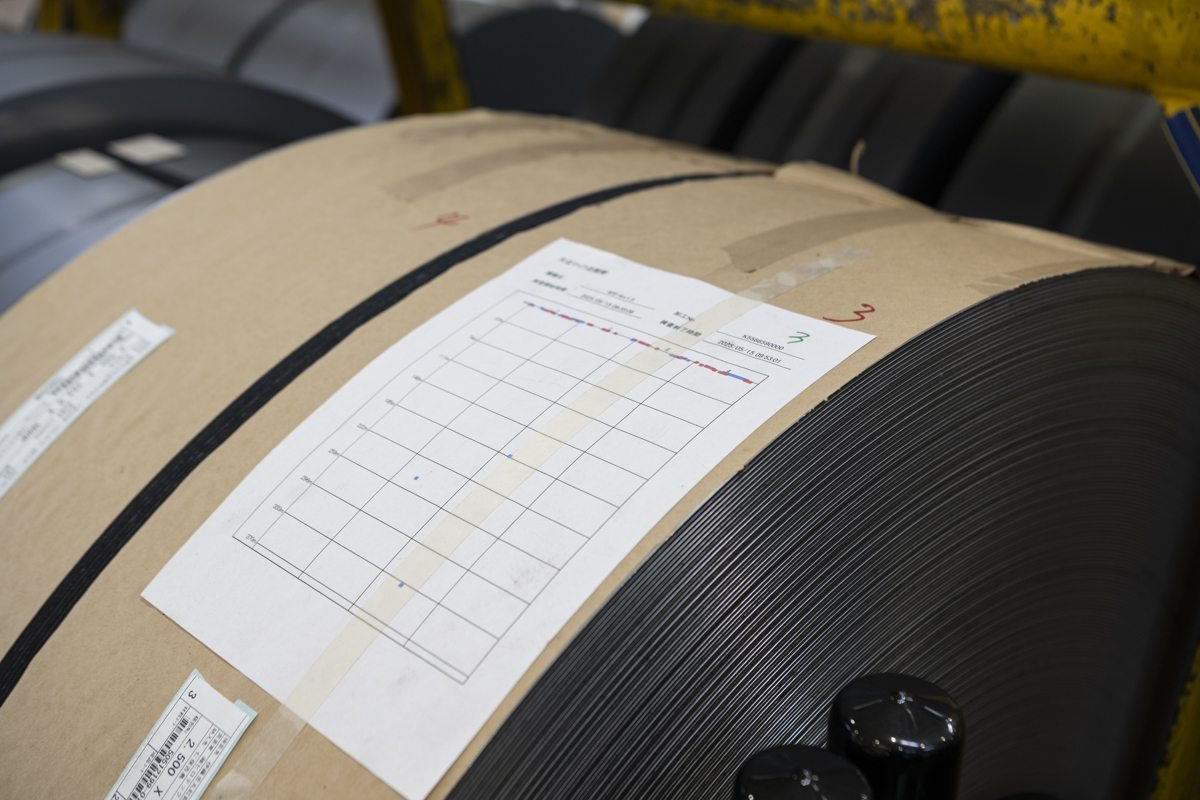
Flaw data attached to the stainless-steel material ready for delivery
With FUTEC ORIGIN’s metal surface inspection device, it is possible to output not only the data specifying the location of flaw, but also photographic data for each flaw. We believe these materials can be helpful in performing client support service.
Update for further productivity improvement
Finally, we asked what functions they wish the device to have additionally in future updated version.
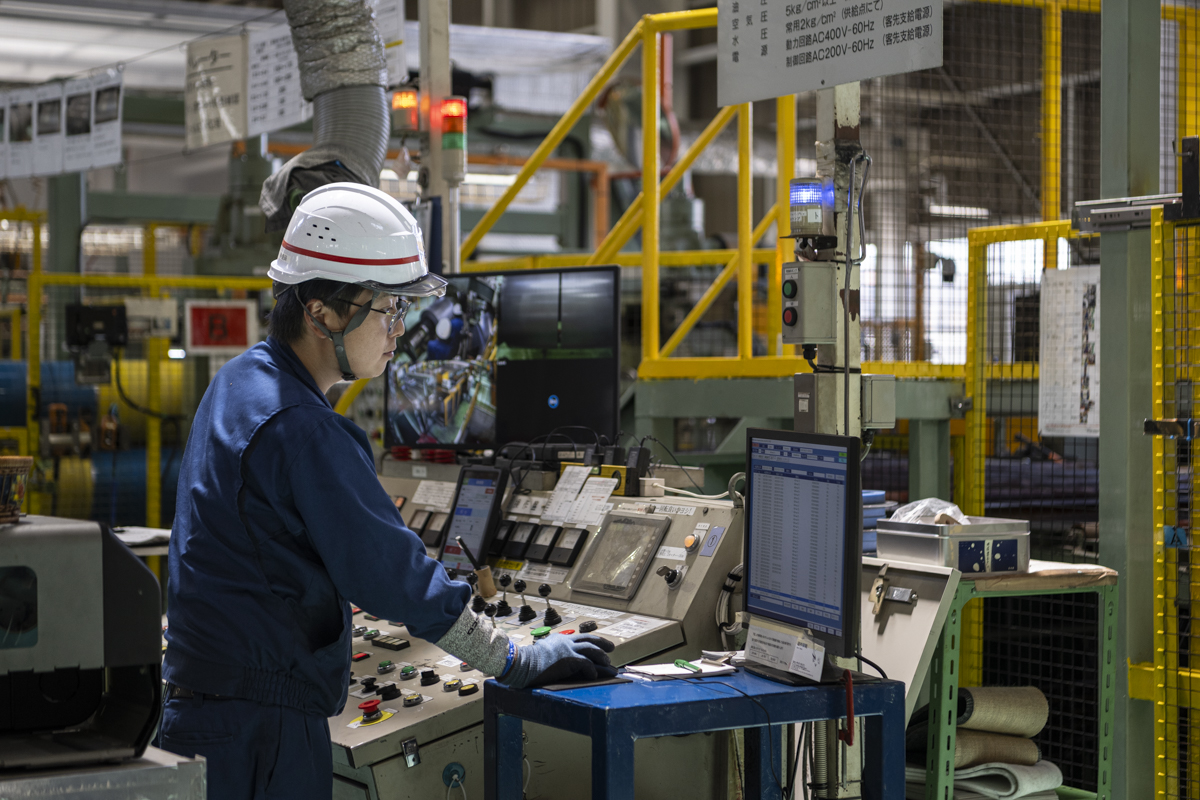
“The current surface inspection device is designed to start manually, instead of automatically, so somebody needs to press the button to start the device. Although only a few times a year, we forget to press the button. We are wondering how this human error can be eliminated.”
FUTEC ORIGIN’s metal surface inspection device is assembled tailoring to each client’s needs. So, even a problem arising a little after the rollout can be solved by performing system update, etc. In this case, the issue may be improved by adding a program that automatically triggers the device to start operation as soon as the stainless-steel material flowing in the production line.
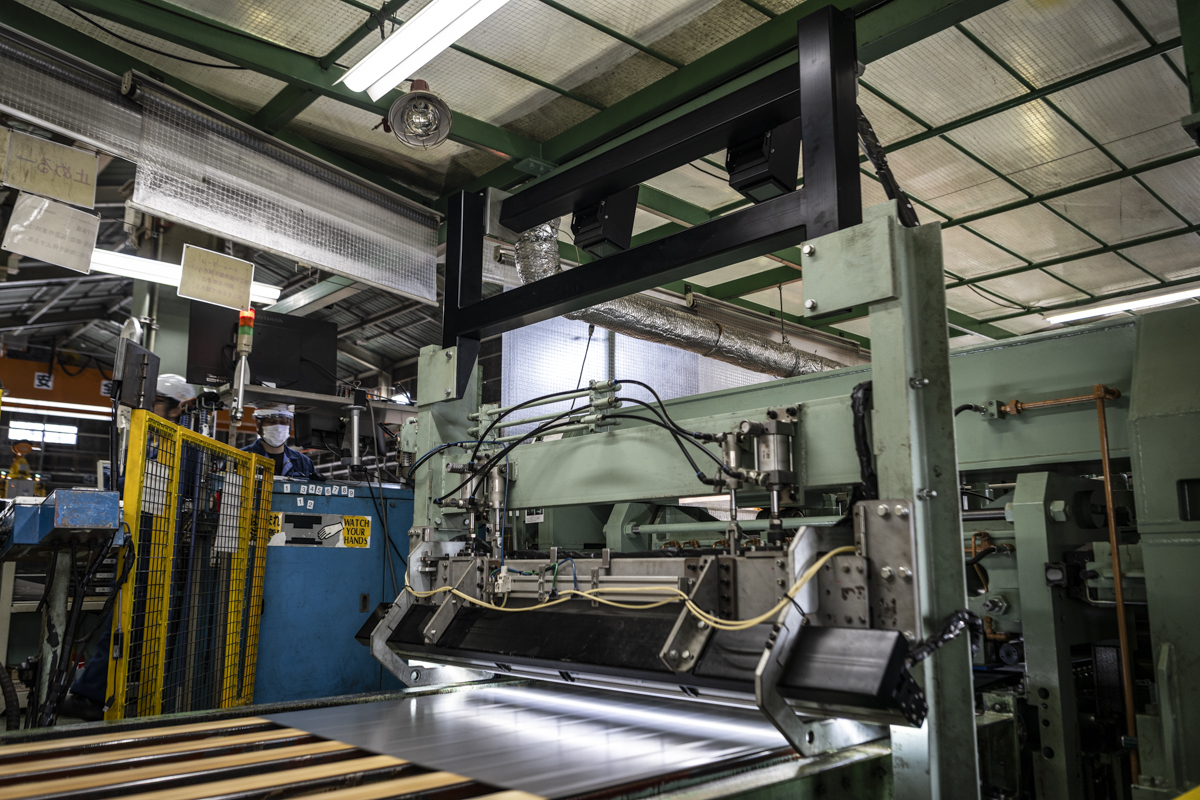
We will continue to help solving problems in the production line and to do our best to support the client’s further improvement of productivity.
If there are any needs of processing automobile steel sheet or stainless-steel material, consult with Summit-Benichu Coil Center. While they have always provided high-quality processing service, FUTEC ORIGIN also contributes to maintaining the high quality, to the best of our ability.
To all from Summit-Benichu Coil Center, thank you very much for your time to talk in our interview.